Marco C Bernasconi – Inflatable structure technologies & Arts in space : A synopsis – 2004
Consultant
First published in the workshop Space: Science, Technology and the Arts in collaboration with ESA/ESTEC, 2004
ABSTRACT : “Inflatable” is a generic designation used for different classes of flexible-wall expandable space structures that have been proposed, studied, and used for more than fifty years. We present here a summary introduction to the potential of this technology, discussing the classification of the field’s technologies, structural morphologies and applications, including graphical examples of some possible forms, shapes, and functions as proposed or manufactured. Finally, we review the principal system’s considerations that help assess the usefulness of this type of objects for a specific realization.
1. Introduction
“Inflatable” is a generic designation used for different classes of flexible-wall expandable space structures that have been proposed, studied, and used for more than fifty years.
This presentation intends to serve as an introduction to the potential of this technology, briefly discussing:
– the classification of the technologies
– some possible forms, shapes, and functions
– primary system considerations.
2. Classifications
Since the beginning of space flight, researchers and experimenters have been confronted with the problem of packaging into the restricted volumes available on the carrier vehicles items that they actually wanted to become much greater; and since those beginnings “inflatable” elements were among those proposed to master this challenge (Gatland and colleagues, 1951; von Braun, 1952).
These type of elements are variously referred to, e.g. as pneumatic, textile, membrane structures, or soft goods. In recent years, NASA introduced the “gossamer” expression to label those forms of spacecraft exceptionally low in mass and suitable for packaging into very small volumes, compared to conventional spacecraft: this term applies to inflatable and membrane structures for space use.
Accordingly, that of flexible-wall, expandable structures seems a better term. The initially high compliance of the walls allows the compact packaging and also enables the geometric efficiency of the materials that leads to the low mass, reinforced by the fact that one can design such structures for the space environment, and not mainly to survive the launch phase. With “expandable,” we refer to those structures that are completely assembled at their manufacture site, then folded, stowed, packaged, or otherwise compacted for transport to their operational location, where they are deployed and installed for functional use. The installation sequence may include a rigidization procedure (mechanical, physical, or chemical), or the structure may be set spinning (for rotationally-stabilized objects), or continuously pressurized, etc.
One can sketch a technological taxonomy on the basis of functional characterization, defining four major classes (Table 1): building on these, one arrives at the thematical structure shown in Figure 1. Further, one can consider a description of the field through the structures’ morphology (Table 2): the simplest elements are tubular items with a thin membrane wall that defines a single chamber. Multiple-chamber objects originate with the need for different pressures, or to increase some functional aspect through modularization.
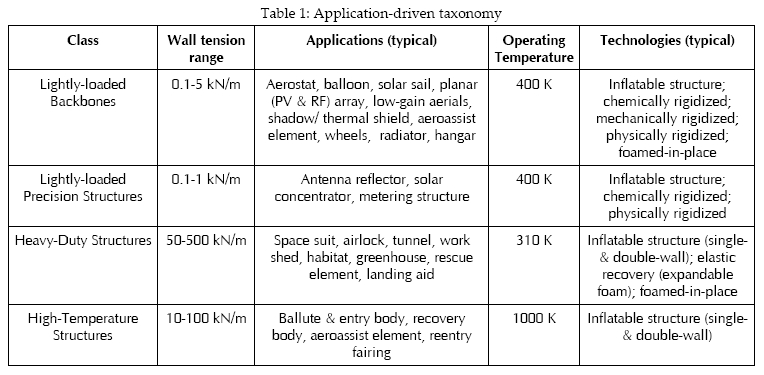
Table 1 : Application-driven taxonomy
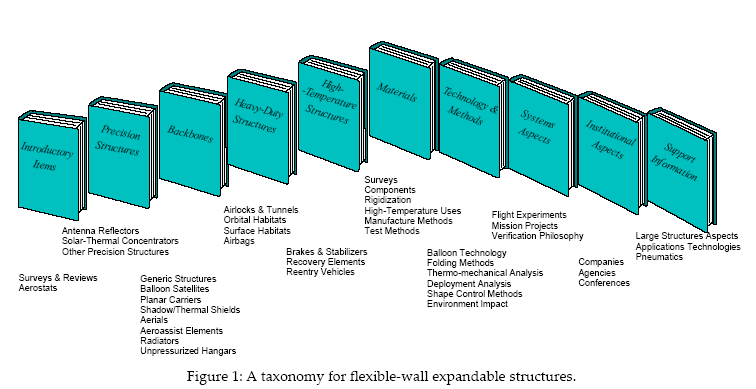
Figure 1 : A taxonomy for flexible-wall expandable structures
Especially for structures subjected to larger loads or with particular shape requirements, the use of double-wall constructions has been studied (see Figure 2 for some major types). Double-wall designs can also lead to multiple chambers, or multi-cellular (Sakamoto, Ishimura, Natori & Higuchi, 2000), elements that offer high resilience and are especially appreciated for architectural uses.
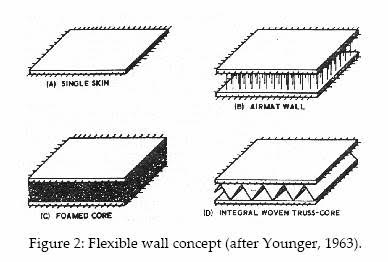
Below, we use some of the project developed by the author to illustrate the morphological possibilities of this approach – as well as its applications’ variety.
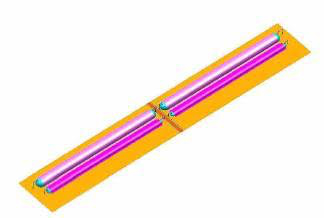
Fig. 3 : One dimensionnel items may also consist of cylindrical parts, as used here to support elements for an array aerial (drawing by R Seibold, Contraves).
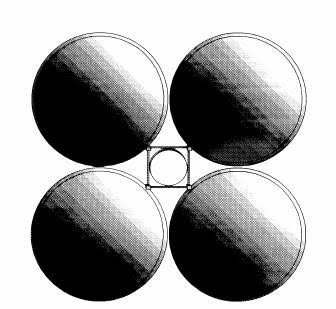
Fig. 4 : Planar elements toroidal structures for the lobed sails of a 10,000-m2 solar-sailing asteroid probe.
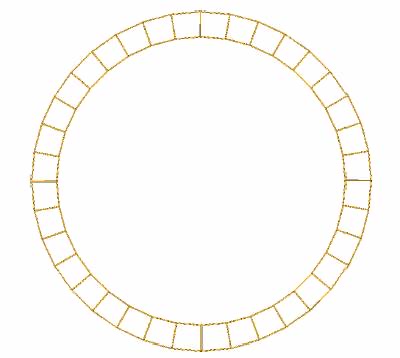
Fig. 5 : The hierarchical use of tubular elements in a truss configuration t create a large ring frame.

Fig. 6. : The OURS Foundation Space Peace Sculpture, with the members connecting ring and central sphere, represent de Simple's form of a single-tier objet (Graphics by AR Woods, TOF)
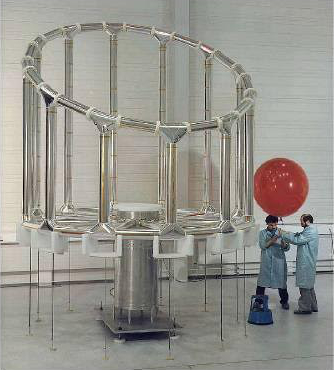
Fig. 7 : A two-tier structure : model of the thermal shield for ESA's original, 8-m FIRST (Contrives photograph).
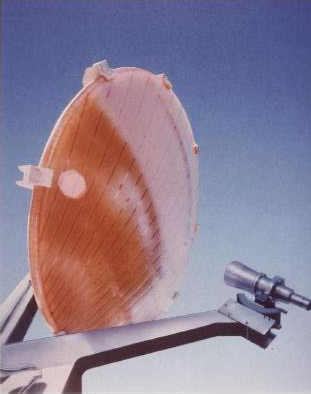
Fig. 10 : Contraves 3.5-m mirowave offset reflector as an examples of a two-chamber design (CSELT picture).
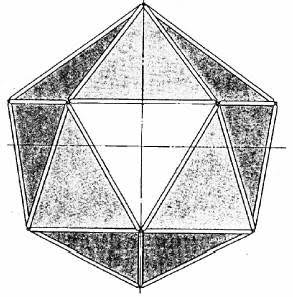
Fig. 8 : An enclosure using an icosahedral skeleton (drawing by R Styner, Contraves).
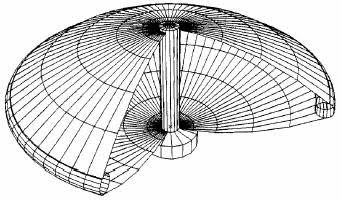
Fig. 9 : Three hammers make a center-fed reflector (here the ESA QUASAT satellite) into a self-supporting cantilever element.
3. Technology
This synopsis cannot even begin to cover the different technological approaches for the diverse range of applications just mentioned. Most generically, flexible-wall structures are rigidized for space operations, to avoid issues like gas replenishment and pressure control: short-life items, habitable elements, as well as aerostatic balloons, form the exceptions.
Most space-rigidized structures to have flown based on the stretching of metal layers (films or wires). But a rather large amount of development work has been invested in chemically-rigidized materials, that remove the last stage of composite structures’ production to the space environment, with associate advantages in the ability to tailor thermo-mechanical and electrical properties of the wall elements.
Other methods would use foam, either as elastic element to deploy and stabilize the walls or as for in-place generation through appropriate chemical reactions. Or let flexible layers harden by drying them out, or by freezing them. Or by creating polymer shape memory materials.
Finally, a current very active research field concerns active structures, where actuators (e.g. piezoelectric elements) are embedded within the thin walls, to control an object’s vibrations or shape.
4. Systems Aspects
When considering flexible-wall structures to fulfill any kinds of function, one has to examine possible layouts and configurations for the deployed object, and to assess the technology approaches that may enable its realization, while considering following systems aspects:
– description of the structure, including its size and mass, as well as its primary structural characteristics (rigidity, stability, …)
– discussion of the folding, packaging, and related launch accommodation aspects (mass, volume, protection/ restraint container, …)
– discussion of the “installation phase,” i.e. residual gas control, release, deployment behavior, pressurization scheme & associated hardware, cure/ rigidization process (as applicable, e.g. thermal design, orientation, timing)
Further specific studies may be already called for in this initial phase of the work; for instance, about the compatibility of possible structural solutions with radio-electrical requirements. For space sculpture projects like OURS, we reviewed the visibility potential of the ring, in terms of magnitude, and ground areas covered, as well as the projected lifetime of the item under various assumption (e.g. configuration, orbital height, …).
Some examples of such design assessment, based of prudent data from existing technology, can be found in Bernasconi (1988, 1994), Bernasconi & Rits (1989), Bernasconi & Zurbuchen (1994).
5. Conclusions
Flexible-wall expandable (“inflatable”) space structures have been proposed, studied, and also used for more than fifty years. Technological approaches exist that allow for the realization of advantageous “large” items for a number of applications – including for cultural and artistic activities in the orbital space.
Acknowledgements – Over many years, many friends and colleagues have contributed help and inspiration for the numerous activities that give the background for this Note, which the author dedicates to the memory of Karl B Bentz, who first introduced him to the world of advanced space inflatables.
Your comments, suggestions, and queries on this theme are welcome at: prudence@bathome.org
Picture credits – NASA (2); Contraves Space (3, 7, 8, 9); AR Woods (6); CSELT (10); Author (1, 4, 5).
6. References
M.C. Bernasconi (1988). Inflatable, Space-Rigidized Antenna Reflectors: Flight Experiment Definition. Paper IAF-88-049 presented at the 39th International Astronautical Congress, Bangalore (India), October 8-15.
Marco C Bernasconi (1994). Design Rules for Expandable Support Structures for Near-Term, Large-Area Applications. Paper 94-F3-098 presented at the Deutscher Luft- & Raumfahrtkongress/ 1994 DGLR Annual Meeting, Erlangen (Germany), October 4-7, published in DGLR Jahrbuch 1994- I, 581-590.
MC Bernasconi & W.J. Rits (1989). Inflatable Space Rigidized Support Structures for Large Spaceborne Optical Interferometer Systems. Paper IAF-89-338 presented at the 40th International Astronautical Congress, Torremolinos (Spain), October 7-13; also: Acta Astronautica 22, 145-153.
Marco C Bernasconi & Thomas Zurbuchen (1994). Lobed Solar Sails for a Small Mission to the Asteroids. Paper IAA-L-0709 presented at the IAA International Conference on Low-Cost Planetary Missions, Laurel (MD), April 12-15; also: Acta Astronautica 35S, 645-655.
Wernher von Braun (1952). The Mars Project (in German). Weltraumfahrt special issue.
KW Gatland, AM Kunesch, & AE Dixon (1951). Minimum Satellite Vehicles. Paper presented at the 2nd International Astronautical Congress, London (UK), September 7; also: JBIS 11[], 287-294.
DG Younger (1963). The Shape of Things to Come in Expandable Spacecraft. Paper presented at the 1st Aerospace Expandable Structures Conference, Dayton (Ohio), October 22-24; Proceedings, 10-61.
© Marco C BERNASCONI & Leonardo/Olats, mai 2004, republished 2023
Leonardo/Olats
Observatoire Leonardo des Arts et des Techno-Sciences
À propos / About | Lettre d'information Olats News
Pour toute (re)publication, merci de contacter / For any (re)publication, please contact Annick Bureaud: info@olats.org
Pour toute question concernant le site, merci de contacter / For any issue about the website, please contact: webmaster@olats.org
Design Thierry Fournier
© Association Leonardo 1997-2022